硅膠材料制品企業(yè)廠家的生產(chǎn)技術(shù)工藝之模具設(shè)計(jì)結(jié)構(gòu):1、模具進(jìn)行厚度達(dá)到上限 ,暫定250mm,尺寸范圍可達(dá)500X500,產(chǎn)品在模具區(qū)最大可做到400X400。硅膠制品廠吸附作用主要是物理吸附,可以再生和反復(fù)使用。在堿金屬硅酸鹽(如硅酸鈉)溶液中加酸,使之酸化,再加入一定量的電解質(zhì)進(jìn)行攪拌,即生成硅酸凝膠;或者在較濃的硅酸鈉溶液中加酸或銨鹽也能生成硅酸凝膠。硅橡膠制品具有開放的多孔結(jié)構(gòu),能吸附許多物質(zhì),是一種很好的干燥劑、吸附劑和催化劑載體。模具產(chǎn)業(yè)結(jié)構(gòu)分析一般分上模,下模,底板,頂板,頂桿、模芯、鉸鏈及其它一些輔助工作零件。在硅膠作為產(chǎn)品設(shè)計(jì)時(shí)應(yīng)注意其模具及生產(chǎn)加工工藝的特點(diǎn):
脫模:硅膠產(chǎn)品的脫?芍苯訌(qiáng)制脫模。 對(duì)于沒有設(shè)計(jì)缺陷的產(chǎn)品,強(qiáng)制脫模的尺寸要求主要是脫模時(shí)模芯最大周長與最小縮頸周長的比值,55以下的產(chǎn)品可以達(dá)到2-3倍。 在需要強(qiáng)制脫模的地方,開口處不得有裂縫或尖角。 因?yàn)楫?dāng)硫化時(shí),需要180攝氏度的溫度,脫模工作幾乎是手動(dòng)的,除了模具本身的上部和下部。 因此,在設(shè)計(jì)零件時(shí)應(yīng)考慮拆卸的方便性和速度。 以避免脫模時(shí)間過長對(duì)零件固化質(zhì)量和生產(chǎn)效率的影響。 由于硅膠脫模方式主要是手動(dòng)脫模,且其頂板的移動(dòng)行程很小,因此硅膠模具與塑料模具相比沒有傾斜的頂部。 通常,不提供抽芯。 3、模芯的固定:與塑料模具不同的是,硅模具的模芯通常在打開模具取下零件時(shí)與產(chǎn)品零件一起取下。 因此,與塑料模具相比,處理模芯的固定和精確定位更加困難,并且模芯的剛性更高。 通常,芯是一起制成的,所有的芯一次固定。 或者使模芯通過輔助工具,以便能夠快速定位。 因?yàn)樵诤夏_^程中有很大的壓力,所以防止模芯移動(dòng)。 4.抽芯:一般不能自動(dòng)移動(dòng),可強(qiáng)制取芯,抽芯僅用于小型結(jié)構(gòu)。 抽芯的設(shè)置與塑料模具相似,但在打開模具時(shí)手動(dòng)取出。 另外,抽芯在模具中占據(jù)較大空間,這不僅工藝復(fù)雜,而且在具有多于一個(gè)模具的硅膠模具中模具空間的利用率低。 盡可能不抽芯。 5.形狀:有機(jī)硅制品在表面完好時(shí)具有很強(qiáng)的韌性,但一旦出現(xiàn)裂紋,裂紋在外力的作用下會(huì)迅速膨脹。 換句話說,有機(jī)硅產(chǎn)品對(duì)裂紋非常敏感。 考慮到這些問題,在硅部件的設(shè)計(jì)中,應(yīng)注意在所有位置都不應(yīng)有尖角,以避免由于應(yīng)力集中而產(chǎn)生裂紋。 開口處的角度R不應(yīng)小于0.5。 6.自除邊:自除邊的主要功能:容納多余的橡膠材料;便于模具排氣;便于修邊。 自去除邊緣通常由零件分離表面處的薄邊緣和相應(yīng)較強(qiáng)的撕裂邊緣組成。 薄邊厚度為0.1~0.2,撕裂邊厚度為0.8,寬度為1~2MM。 7.嵌件:硅膠制品加工時(shí)可放置各種類型的嵌件,但應(yīng)注意以下問題:一是預(yù)埋件表面應(yīng)進(jìn)行預(yù)處理,主要是表面硫化或表面活化。 否則,將難以牢固地連接插入件和膠部件。 另一個(gè)是插入件的固定和定位,其可以在垂直方向上的一個(gè)方向上固定,但必須在所有其他方向上固定。 在整個(gè)模具過程中避免鑲塊移動(dòng)。 第三,鑲塊周圍的膠水厚度。
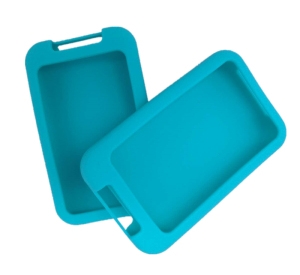